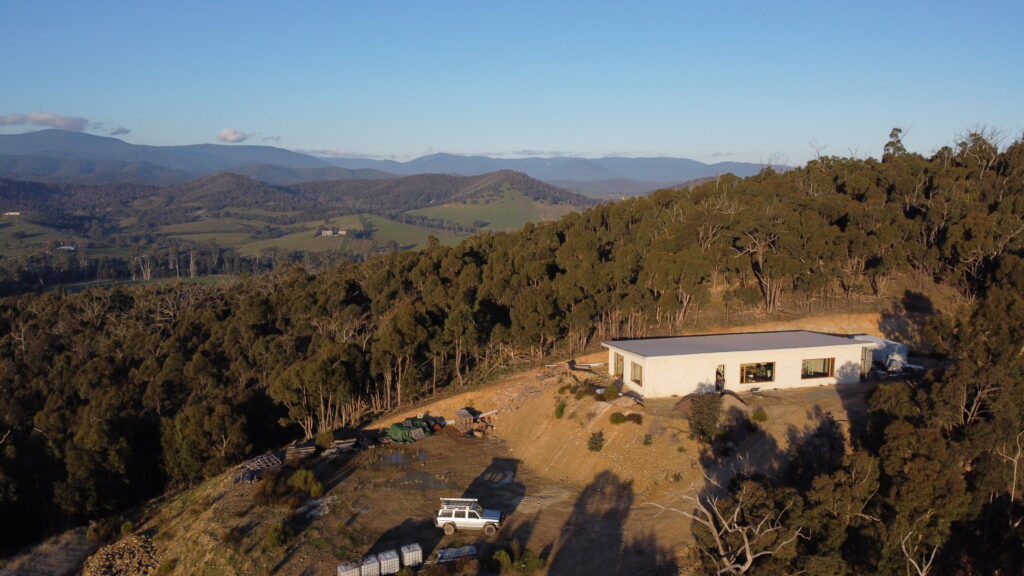
Wow, what a ride the past few months has been. We have finally returned to our home in Melbourne, after 5 months on WorkAway exchanges. We started our WorkAway journey at Murrnong Farm, followed by a short stay at Chestnut Farm, and completed it last week after 2 months working on a strawbale house build in the Yarra Valley.
Our hosts were an older couple who purchased land in Steels Creek several years ago, from people who had lost their house in the 2009 Black Saturday bushfire. They are owner-building a strawbale house, on an incredibly difficult site but with spectacular views. We were interested in working on their build to gain experience for building our own strawbale house in the future. We certainly learned a lot, coming up against many challenges and having to work through solutions. It gave us a real taste of what being owner-builders is like, and we learned that it’s most certainly not for the faint-hearted. That said, we’re now more keen than ever to get to work on our own place.
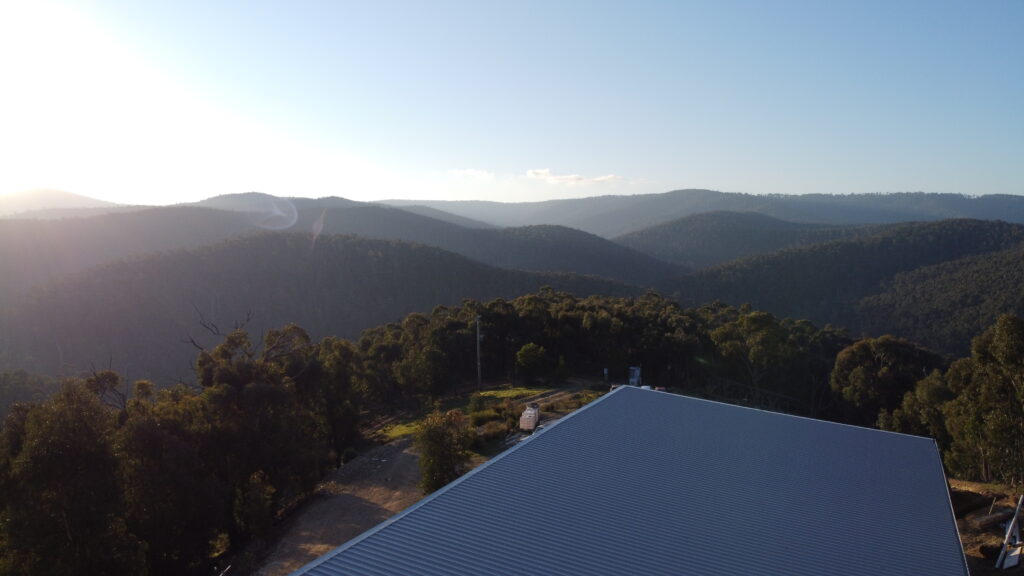
Strawbales have been used for building for over a century, and have amazing insulation properties. For those who aren’t familiar with the “R-value”, it’s the Thermal Resistance Rating, which determines a given material’s ability to resist the transfer of heat. A higher R-value reflects better thermal resistance. The R-value of strawbale walls is 8 to 10, compared with R1.5 for timber framed insulated walls, R2 for insulated brick veneer, R0.5 for uninsulated brick veneer, and R1 for mud brick. For those of us that live in colder climates, you really can’t beat it, which is why we plan to build with strawbale for our future home. Strawbale is also suitable for building in fire prone areas and can be built in areas with a Flame Zone BAL rating – as the one in Steels Creek is.
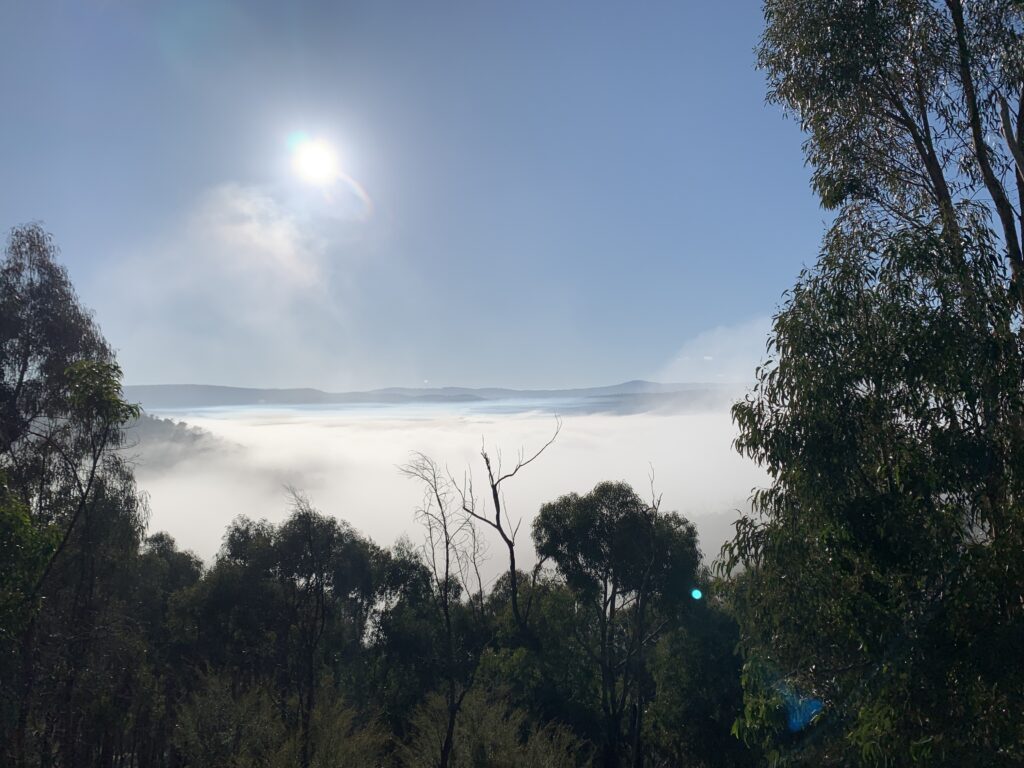
Working with natural materials presents a range of challenges which require unique, on-the-fly solutions. Materials aren’t uniformly sized to the millimetre, for example, so there’s often some problem-solving involved at edges and joins. For me personally, nothing beats the aesthetic of a natural home, whether it be strawbale, mud brick or cob. Earthen floors and render are simply stunning to look at, and living in a home with pretty much zero toxins and minimal embodied energy aligns with our values for reducing our impact on the planet.
The past couple of months have given us invaluable insight into the processes involved in owner-building. Before this WorkAway, all our research had been theoretical, but since gaining the hands-on experience we feel prepared enough for our own build. For anyone interested in building their own home, I thoroughly recommend volunteering on someone else’s build first. It’s one thing to do a weekend-long course to learn some hands-on building skills, but spending a month or two on an actual build gives you insight you really couldn’t gain any other way. Plus, you get to learn from other people’s (sometimes very expensive) mistakes, and build problem-solving skills to deal with the inevitable challenges that will arise.
There’s so many resources for people interested in following this path. I’ve listed a few of the ones I’ve found particularly helpful as a starting point. If you have any resources to add to this list please hit us up in the comments!
USEFUL RESOURCES FOR OWNER-BUILDERS
– Undercover Architect Podcast and Blog
– The Owner Builder Club (Australia) Facebook group
– YourHome – The Australian Government guide for sustainable homes
– SketchUp – the Pro version is available as a free 30 day trial, and I used this to draft a 3D model of our future home. It’s great fun, and helps you visualise your future house